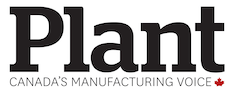
Employee engagement: create owners and form natural work groups
By Richard Kunst
Industry Operations Production Manufacturing Employee Engagement engagement manufacturing OperationsManage rules, create owners out of employees and organize natural work groups to enhance the benefits of lean.

Make the most out of the employees “Gift of Time.” PHOTO: FOTOLIA
In The Fearless Monkey author Dennis Heijin dedicates a portion of the book to the importance of providing customer service and how corporate rules can diminish the ability of an organization to deliver. He proposes the need for rules management.
A principle of lean is how to increase employee engagement; or how to encourage them to act as “owners”, something that this example of customer interaction did not demonstrate:
A retail store did not have sufficient stock of an item, but the Customer Service Desk did offer to order more for 40% in advance; however, it would take four to six weeks for delivery to the store. The customer service rep was asked if the store could call with a more precise delivery time once the replenishment order was made? “No, they didn’t have the time to do that!”
“Customer service” lost that retailer a significant order that was subsequently filled online.
Every value stream should be viewed and critiqued through the eyes of the customer, but you should also review the rules. They may make sense in many situations, but how much can they be bent to satisfy customers?
Internal value streams focus on continuous process improvement and ensuring employees don’t waste time on frivolous activities. But look at employees through a different lens, and you’ll see they’re providing you with their “Gift of Time,” a non-renewable resource that – once used – becomes experience.
How you treat them reflects how they perceive their standard of the standard of performance, even if the rules support something different, and it starts even before the beginning of the workday. How appealing is the employee entrance and the cafeteria? Is it well organized, clean and does it project professionalism? These attributes act subliminally on employees.
For example, a company that made components for the food industry needed to improve internal quality performance. It adopted simple good manufacturing practices (GMP) rules: no jewellery, and employees were required to wear hair and beard nets. Within days, quality dramatically improved, which was attributed to increasing the level of expectations conveyed through the GMP requirements.
This pride in the brand continues into the workplace. A clean, organized and well engineered work environment channelling 5S+1 allows employees to deliver professional results without searching for the proper tools or incurring any of the other eight deadly wastes.
And never underestimate what the “Gift of Time” can deliver. During a turbulent business cycle, a company workforce facing layoffs was challenged to improve materials yields as a way to offset the need to reduce labour. During a 30-day window employees found and implemented enough changes to more than offset the need for labour reduction. All of this plus first time quality, delivery performance and throughput improved, making the company more competitive.
Other lean attributes also deliver benefits. Teams conduct reflections while establishing goals during daily quick stand-up meetings. Total productive management is a nice pre-cursor to standardized work, while acting as an alarm clock for the human brain to insure a safe secure and comfortable environment is maintained. Policy deployment keeps teams aligned to a common goal, and visual standard work instructions share current best practices.
Creating a team
One of the silent covenants of lean is to create an environment where the employee works without disruption. It’s all about muscle memory. An employee engrossed in a process develops a rhythm that’s like a dance.
When you put employees together social dynamics lead to four phases that develop them into a team: forming, storming, norming and performing. Watch for it, understand it and wait for the evolution to transpire.
Empowering natural work groups allows the team to self govern and deliver outstanding results without the need for command and control.
Structure and support consists of small groups of employees, geographically close, that share defined operational and continuous improvement tasks to achieve common goals. Work groups and organizational support groups operate with clearly defined roles and responsibilities.
Natural work groups go through a transition process before operating as a unified, empowered team. The transition needs to be understood by plant leadership. The number of phases as well as the required time will depend on the current level of workforce engagement and on the natural work group vision defined by the leadership. A strong indicator of the group’s readiness for transition is their effectiveness in achieving performance goals (health and safety, quality, throughput, productivity and continuous improvement). These should be closely monitored and serve as the basis for the entire process.
The group needs to be quantified. Supply them with a “report-out board” that covers:
- monitoring daily progress to achieve goals and objectives;
- job rotation and multi skill development;
- quality compliance;
- safety;
- suggestions for improvement;
- product enhancements;
- employee attendance, which indicates engagement; and
- rumour dismissal.
Fully engaging employees as owners of the business, creating natural work groups and reinforcing their efforts by deploying lean strategies will ensure manufacturing activities are successfully accomplished.
Richard Kunst is president and CEO of Cambridge, Ont.-based Kunst Solutions Corp., which helps companies become more agile, develop evolutionary management and implement lean solutions.