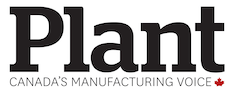
Automation: Solving the talent shortage or exacerbating it?
Sadi Muktadir
Innovation & Technology ManufacturingManufacturers are looking to add personnel in order to address the talent shortage, however, 2021’s Advanced Manufacturing Roundtable showed a different approach of how manufacturers were addressing the decrease in personnel.

Photo:© Blue Planet Studio / Adobe Stock
The numbers don’t lie. According to a 2021 study by The Manufacturing Institute and Deloitte, 77 per cent of manufacturers say they will have ongoing difficulties in attracting and retaining workers in 2021 and beyond. This is on top of a separate study by ManpowerGroup showing that the manufacturing sector in Canada is looking to increase hiring by at least 50 per cent in the Q4.
This response to a recovering pandemic economy doesn’t come without some other suggested solutions. While there are many manufacturers looking to add personnel and address the talent shortage, 2021’s Advanced Manufacturing Roundtable painted a different picture to how manufacturers were addressing the decrease in personnel.
“Being required to function with a smaller number of people has shown manufacturers that they actually can, and once they figured out a way to do it with IIoT investments, they discovered the benefits of reduced staff requirements,” said Peter Coffee, VP for Strategic Research, Salesforce.
The roundtable’s discussion was focused around how advanced technologies and IIoT investments have helped manufacturers respond to talent shortages plaguing the industry.
Canadian Manufacturing’s own 2021 survey found that 28 per cent of manufacturers reported that they were able to use their technology upgrades to reduce staff requirements. This was the third leading benefit of their upgrade, up significantly from recent years. Even more significant, was that 36 per cent of manufacturers currently applying IIoT-connected solutions reported experiencing the benefit of reduced staff requirements.
Increased profit margins, quality control, reduced downtime and increased throughput are all some of the benefits seen from reduced staff requirements; something manufacturers are beginning to explore.
“Reduced staff is a big part of any sort of technology investment, especially with regards to IIoT connectivity. The whole point is that you’re investing to give your staff the ability to do more with less,” said Peng-Sang Cau, VP, ATS Automation.
Though automation technologies and Industry 4.0 tools are helping manufacturers do more with less, manufacturing executives and researchers recognize that it’s not enough to address the shortage.
“People are investing in technology because of the labour shortage but the labour shortage is still a huge issue that hasn’t gone away,” said JP Giroux, President, Excellence in Manufacturing Consortium (EMC).
Canadian Manufacturing’s own 2021 survey found that 28 per cent of manufacturers reported that they were able to use their technology upgrades to reduce staff requirements. This was the third leading benefit of their upgrade, up significantly from recent years.
Dennis Dussin, President, Alps Welding Ltd. expanded on this.
“During COVID-19 lockdowns, every business has had to get more done with fewer people, but the labour shortage has gotten worse. I think it’s much worse after COVID-19 than it ever was before the pandemic. We were always trying to get by without enough skilled labour, and with the pandemic that’s gotten worse. We’re looking for ways to get more done with fewer skilled people and technology’s a big part of that.”
Steve Bassaw, Product Manager, SYSPRO illustrated how strained the labour market is in his work with clients.
“We have clients who want to expand their plant, they have the money, and the resources but the only thing they don’t have is the labour. Even worse, they’re ready to build a second plant and the only constraint is that they can’t find the labour. This is a story we’ve been hearing for years now, long before the pandemic.”
While technology may be a necessary and helpful investment, it’s clear that other strategies are needed in order to address the talent shortage.
“There’s a lack of skilled talent to address the new technologies being integrated. This is related to our own inability as a sector to attract the next generation of talent,” said JP Giroux.
Scott McNeil-Smith, VP of Manufacturing Sector Performance, EMC added onto this.

Photo:© Blue Planet Studio / Adobe Stock
“People are still the driver, regardless of the technologies being implemented. One of the big challenges, especially for smaller manufacturers is finding internal subject matter experts and consultants to help grow the company.”
Manufacturing executives believe that with the increase in automation and advanced technologies helping manufacturers, so too does the need to rise to attract and retain talent.
“The customers I’ve been talking to are citing challenges in finding people. They can’t hire fast enough so they’re trying to leverage new technology because that’s what Millennials and Gen Z are interested in. They’re not interested in old-school manufacturing. And the companies that are more progressive with their technologies are able to attract and retain some of those young people,” said Rory Macleod, Area VP of Sales, Salesforce.
Manufacturers understand that solving the talent shortage requires catering to that talent through those investments in new technologies.
“If anyone is going to solve this labour shortage it’s not going to be anyone here on this call. It will be the next generation, and solving that shortage depends on our ability to get those young people with digital skills into the industry,” said JP Giroux.
It won’t take technology alone to solve the talent crisis.
____________
Sadi Muktadir is the Editor of Canadian Manufacturing.