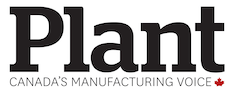
Go with the flow pocket-sized
By PLANT STAFF
Innovation & Technology Manufacturing Endress manufacturing TechnologyMeasurement device mounts directly before or after pipe bends.

Mounts before or after pipe beds.
PHOTO: ENDRESS+HAUSER
Picomag has been enhanced with temperature compensated conductivity measurement and increased accuracy from ±2% to ±0.8%.
Endress+Hauser’s pocket-sized flow measurement device needs no inlet/outlet runs, so it mounts directly before or after pipe bends. Configuration data is exported as a PDF for archiving in a computer or mobile device.
Configure in the field via Bluetooth and SmartBlue App with a commissioning wizard. A user-friendly, auto-rotatable 1.4-in. display automatic adjusts to the mounting position. Select analogue or digital communications with IO-Link, which reduces the complexity of connecting simpler devices to any fieldbus system.
Picomag comes in a range from DN 15 (1/2 in.) to DN 50 (2 in.) where the focus is on high repeatability (±0.2% ofs) and reliable measured values.
It’s suitable for process temperatures between –10 to (temporarily) 85 degrees C, and process pressures up to 16 bar (232 psi). It installs into any pipe up to 50 millimetres (2 in.) in diameter, even in confined spaces.
Endress+Hauser Canada Ltd., based in Burlington, Ont., is a supplier of measurement instrumentation.
This article appeared in the November-December 2020 print edition of PLANT Magazine.